Water pollution abatement facility examines available technologies for dewatering mixed raw biosolids
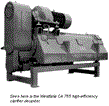
When facility officials investigated alternative technologies to vacuum filters, they found a separator that not only saves money on disposal and treatment costs, but also required less power, chemical use and operator attention.
The Haverhill, MA water pollution abatement facility is a midsize plant, treating about 10 million gallons per day (mgd). The plant was using vacuum filters to dewater biosolids, and combined with lime and ferric chlorine, officials say they were getting ‘less than satisfactory results.’ Besides high maintenance requirements, this method resulted in very wet cakes.
The resulting sludge was trucked to landfill sites, and disposal costs were high—and projected to triple. Looking ahead, officials were concerned that vacuum filters would not meet the newer regulatory compliances.
Examining alternative technologies
Facility Manager John Connor and Superintendent William J. Pauk decided it was time to look into alternative technologies. Belt filter presses were tested along with several different manufacturers' centrifuges.
After thorough testing of the alternative options, it was learned that a separator model CA 755 decanter, manufactured by N/A (Northvale, NJ), consistently outperformed the alternatives.
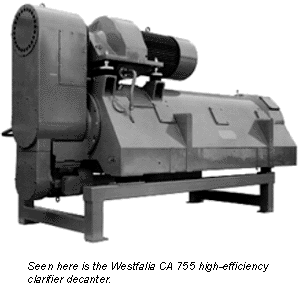
Westfalia Separator centrifuges are designed for continuous operation with minimal operator attention. They have flow rates for dewatering of 150 to 600 gpm, and there is no need to use lime for bulk.
The decanter centrifuges produce cakes that are 25% to 35% dry solids (see Table 1). Drier cakes mean less volume for disposal. And the process is totally contained, so there is less odor to deal with. Compared to vacuum filters the centrifuges take up less space and require less operator attention.
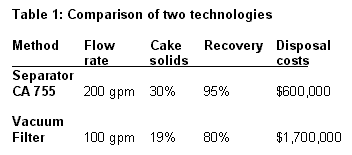
Drier cakes was greatest benefit
"The main benefit was drier cakes. The reduced volume of sludge translated to immediate savings for us in terms of our disposal costs. We went from 140 wet tons to only 55 wet tons per day. This alone saves on equipment power, repair, chemical and disposal costs, and so on. Our disposal costs went from a projected $1.7 million to $600,00 per year. There are other cost savings as well. There's no expense for lime, as it is not needed for this treatment method, not to mention the savings in operation and maintenance costs," says Connor.
For more information on this or other Westfalia Separator Inc. products, visit the company’s storefront.
Visit the Water Online Buyer’s Guide for more product information on Separators.
Edited by Tracy Fabre
Managing Editor, Water Online