Stability and Linearity: Keys to an Effective Measurement System
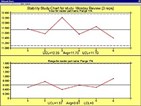
This primer explains what stability and linearity are – and their roles in a measurement system.
By Gordon K. Constable, PQ Systems, Inc.
Knowing that a measurement system is stable is a comfort to the individuals involved in managing the measurement system. If the measuring process is changing over time, the ability to use the data gathered in making decisions is diminished. If there is no method used to assess stability, it will be difficult to determine the sensitivity of the measurement system to change and the frequency of the change. Calibrations and R&R studies provide some information about changes in the measurement system, but neither provides an accurate picture of what happens to the measurement process over time.
Stability is the Key to Predictability
In terms of measuring equipment, stability is determined by using a control chart. Repeated measurements are obtained using a measurement device on the same unit (frequently called a master) to measure a single characteristic over time. As measurements are taken, points within the limits indicate that the process has not changed and the prediction is made that it is not likely to change in the future.
The appropriate time interval is often a major consideration when analyzing the measurement system. Knowledge of the circumstances and conditions in which the equipment is used will help identify special causes when the system is unstable. Action should be taken to make the measurement system robust to the conditions that cause instability. The more likely it is that the measurement system will change, the shorter the interval should be between measurements.
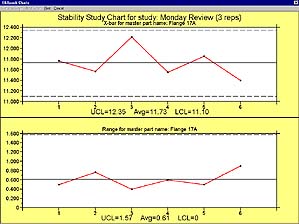
The Role of Linearity
In addition to using control charts and understanding the concept of stability for the measurement system, determining the linearity of the measurement system and understanding its impact on the measured values will contribute to the effectiveness of the measurement system. Linearity is the difference in the accuracy values through the expected operating range of the equipment. It can be determined by selecting parts throughout the entire operating range of the instrument. The accuracy of the parts is determined by the difference between the master measurement and the observed average measurement, which can be done by plotting the accuracy values from the smallest size (closed position) to the largest size (open position). The slope of a "best fit" line through these points represents the linearity of the equipment. This best fit line is determined by using least squares regression.
If equipment demonstrates non-linearity, one or more of these conditions may exist:
1. Equipment not calibrated at the upper and lower end of the operating range
2. Error in the minimum or maximum master
3. Worn equipment
4. Possible review of internal equipment design characters
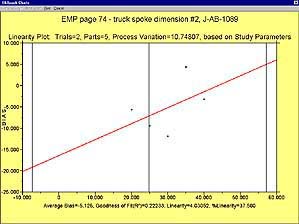
Conclusion
Product and process conformance is determined by measurements that are taken by a measurement system. Errors in these measurements have a direct bearing on conformance as defined within the system. A clear understanding of the results of the measurement system requires an understanding of the possible error within the system. To understand this error, one needs to understand the terminology, and in particular, the concepts of stability and linearity.
For more information, contact PQ Systems, Inc., 10468 Miamisburg-Springboro Rd., Miamisburg, OH 45342. Tel: 800-777-3020; Fax: 937-885-2252.
Gordon K. Constable, Ph.D., a PQ Systems trainer and consultant, has had more than 20 years of experience in consulting and training in statistical process control and measurement systems analysis for organizations in automotive, process, manufacturing, chemical, and machine tool industries. He is a Certified Quality Engineer, Certified Quality Auditor, and Certified Production and Inventory manager.