Renishaw's Non-contact Laser Toolsetter Measures 'at Speed,' Checks for Dynamic Errors
The new NC1 laser-based toolsetting system from Renishaw Inc. (Schaumburg, IL) delivers the benefits of high-performance non-contact toolsetting for the rapid measurement of tool length and diameter. The system brings faster speeds and increased productivity as well as easy installation and minimal maintenance.
Unlike static toolsetters, the NC1 system measures tools "at speed" to get spindles into cut faster and checks against dynamic errors using advanced electronics and simplified hardware design. It uses a laser beam to rapidly measure tool length and diameter at normal spindle speeds, which minimizes the impact on cycle times. Contrary to how touch-type toolsetters operate, the NC1 doesn't need to stop the tool or slow down CNC axes. Laser checking at working spindle speeds identifies dynamic errors caused by clamping inconsistencies and radial runout of the spindle, tool, and toolholders.
The NC1 also performs broken tool detection on-the-fly at rapid traverse, which further reduces out-of-cut time. This feature is particularly useful on unattended machining operations where tool damage can cause costly scrap or rework. After each machining operation, tools can be passed through the NC1's laser beam at rapid feed rates to check for damage. Each facet of multifaceted tool can be checked.
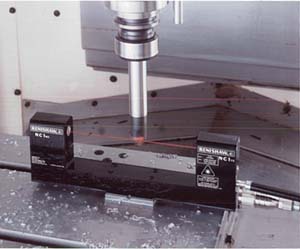
As the tool moves through the laser beam, system electronics detect when the beam is broken and sends an output signal "trigger" to the controller; this allows the position of tips, teeth, or cutting edges to be quickly established. The system triggers when the laser beam is broken beyond a 50% threshold by the tool being checked. Tools as small as 0.2 mm can be measured anywhere along the beam, and the non-contact measurement avoids possible damage on delicate tools.
The toolsetting system employs the company's resident control software to set most common types of tooling including static setting of drills, rotating length setting of tools such as face mills, and rotating diameter setting of slot drills and boring bars. Software macros store the various trigger locations and perform calculations to establish tool length and diameter. Other macros allow for broken tool detection, insert verification, and thermal compensation.
The laser is generated using a diode-based laser system that's deemed reliable for machining conditions. The visible-red laser operates at 670 mm wavelength at low-power output less than 1 mW. Positive internal air pressure is used to keep out debris and coolant, which brings a continuous stream of air through the laser beam to shield the optics from contaminants.
With no moving parts, the NC1 can operate virtually maintenance-free. The complexity of shutters, switches, and solenoids (typically found on other non-contact designs) is eliminated and there's no need for PLC or CNC executive software modifications. The design also ends the need for brackets or actuators usually required to fit contact-based toolsetters to horizontal machining centers. The company's "virtual pivot" system enables simple and quick beam alignment.
The NC 1 system is supplied in ranges up to 2 m to fit practically any size and configuration of machine tool without affecting the work envelope. It also can be retrofitted to existing machines.
Renishaw Inc., 623 Cooper Ct., Schaumburg, IL 60173. Tel: 847-843-3666; Fax: 847-843-1744.
Edited by Nancy Katz