Portable CMM Improves Quality, Saves Money on Carrier Production
As the U.S. launch site for Metronor's Solo coordinate measuring machine, a manufacturer of carriers and conveyor systems is experiencing greater product quality and satisfying customers.
Contents:
Filling a Market Void
Finding the Right Tools
Quality Throughout the Process
Made for the Shopfloor
Today's OEMs continuously require improved quality and cost efficiency throughout the entire production process and supply chain. To be successful, they're constantly looking for tools and methods to improve their performance. Dearborn Mid-West Conveyor Co. (DMW; Dearborn, MI), takes this approach as well. As the U.S. launch customer for the new Solo portable CMM from Metronor Inc. (Southfield, MI), DMW is showing "improved product quality as well as service that meets all customer expectations."
Filling a Market Void
Combining low cost with large volume capability and ease of use, the Solo portable offers something new. According to the company, "no large-volume portable coordinate measuring machine has been available in the sub-$100,000 market" — until this product. It handles volumes up to 45 ft, exhibits a 2-sigma sphere test, boasts accuracy of less than 0.002 in., and has 3D length accuracy (bias) of 0.004 in. The complete turnkey package costs less than $70,000.
The CMM is able to handle large volumes because of its electro-optical working principle. Here's what happens: A single high-resolution charge-coupled device (CCD) sensor (or camera), works with Metronor's patented smart-LED Light Pen to make direct feature measurements throughout the camera's field of view, which is just like a traditional CMM. Designed to provide easy reach and access in both small and large volumes, the machine has no moving mechanical parts and delivers high long-term stability and reliability.
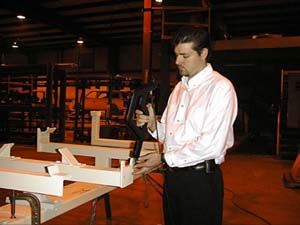
Back to top
Finding the Right Tools
DMW supplies design, engineering, manufacturing, and installation services for conveyor systems to the automotive and other industries. "In order to remain the leader in our field both with regard to product quality, cost efficiency, and customer support, we are constantly looking for improvements — both in the tools we use and the procedures we follow. When we became aware of the Solo, we immediately recognized the very good fit with our requirements and the opportunity for more efficient quality assurance procedures," says Robert Underwood, DMW's MIS manager.
According to Underwood, Solo employs three main characteristics that result in savings: single setup, real-time comparison of product with CAD design, and portability. It can handle even the largest carriers in a single setup, which saves time and improves accuracy. Previously, the company has used articulated arms, which are good systems but can't handle the volumes the company needs to measure.
The second benefit allows the company to compare the actual carrier with the latest-revision CAD design in real time; it also provides immediate graphical results to the operator and engineers. "We avoid the need for inspection blueprints and the problems associated with misinterpretations and outdated revision levels," notes Underwood.
Furthermore, the Solo's portability and easy setup means that it can be used wherever it's needed, either at the DMW facilities or their suppliers' sites. "Our first Solo has been almost constantly ‘on the road' since delivery," says Underwood.
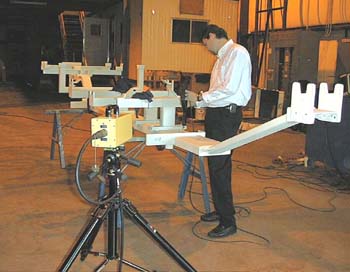
Back to top
Quality Throughout the Process
Tony Rosati, DMW's vice president of the DaimlerChrysler group, believes that the CMM has improved the company's quality throughout the manufacturing process and has helped save money by identifying problems earlier in the process. "For example, we now have a tool to quickly and easily verify that the jigs used to build the carriers match our current CAD design, regardless of the jig's location or size. We can also bring the system into the customer's plant to assist in solving any problems in a constructive and time-efficient manner. Based on our experience so far, we feel that Solo will contribute very positively to our customers' satisfaction with our products and service. Our second Solo unit is now being delivered."
Back to top
Made for the Shopfloor
Metronor, which supplies CCD-based large volume, high precision transportable CMM technology to the aerospace and automotive industries, has been manufacturing high-end electro-optical measurement systems for more than 10 years.
"From the start, SOLO was designed to be rugged, reliable and easy to learn and use, and all components and solutions were chosen to this end. In addition, we were able to make it small, portable and attractively priced," explains Dr. Alf Pettersen, vp of technology at Metronor headquarters in Norway. "So far, the feedback from the market has been very favorable, but we are always looking for ways to improve all our products and appreciate feedback and suggestions from customers like DMW."
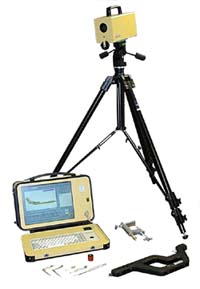
While Metronor has marketed its DCS product (a high-end, dual-sensor system) primarily to automotive and aerospace OEMs and tier-one companies, the new CMM offers broader market appeal. "Bringing Solo to market is a challenge for us, as the SOLO seems to appeal to companies far outside what has traditionally been our core markets," concludes president Harald Suphellen.
Metronor Group, 21652 Melrose Ave., Southfield, MI 48075. Tel: 248-353-3100; Fax: 248-353-3101.
Edited by Nancy Katz