Gantry CMM Performs Double Duty for Injection Molder
The DEA BETA gantry-type CMM from Brown & Sharpe helped this company trim inspection time as well as optimize assembly of its injection molding machines.
When injection molding equipment manufacturer Engel Canada Inc. (Guelph, Ontario) needed to improve inspection time for its product lines, the company turned to a gantry-type coordinate measuring machine to do the job. It chose the DEA BETA SP from Brown & Sharpe, Inc. (North Kingstown, RI).
Engel Canada manufactures injection molding equipment such as injection molding machines, automation equipment, and software for molding thermoplastics, thermosets, BMC, LSR, elastomers, and powdered metals. Products include 35–200 ton hydraulic, tiebar-less and 150–500 ton toggle injection molding machines, along with sprue pickers, pick-and-place handling devices, servo-driven robots, mold mount and change systems, and production monitoring systems. The company also makes systems designed for advanced processing technologies such as gas melt, lost core, and textile melt.
Fitting Right In
The DEA BETA was installed on the machine shop floor to handle large molding machine components that the company works with, such as platens, that are about 1½ m long by ¾ m wide and weigh up to 5,000 kg.
"Our installation is somewhat unique in that we don't have a surface plate or table that we place the parts on," said Steve Schock, quality manager at Engel Canada. "We put the parts right on the floor. The foundation that we're using formerly supported a machining center, and subsequent vibration tests confirmed that we've got a stable pad."
In the machine shop, the BETA SP is installed adjacent to a large grinder — a condition that's about as harsh as it can get for precision measuring equipment, according to Schock. "We've noticed no degradation in reliability or accuracy because of the CMM's location, however," he noted.
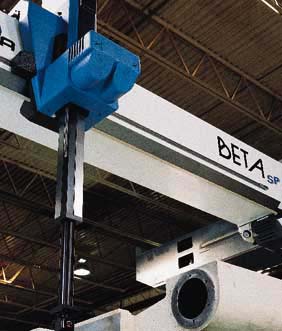
In the past, Engel Canada used a surface plate. Inspectors would stand large machine components on an 8 x 6 x 18 ft table and check dimensions using a height gage. On a first-off inspection of a major part like a platen, more than 1,000 data points might have to be collected to gather the dimensional information necessary for process correction. Dimensional tolerances are tight. Even on large parts, squareness and parallelism tolerances run in the neighborhood of 0.03 mm. It was a time-consuming process; some parts took up to four hours to do.
More Data More Quickly
The Brown & Sharpe DEA BETA is a medium–sized gantry CMM designed to operate with high accuracy and reliability in an open shop environment. Its aluminum machine structure quickly adapts to temperature changes, and scale readings are unaffected by changes in the machine structure caused by thermal gradients. Fully covered ways protect the machine from airborne contaminants.
The open design of the BETA SP allows easy integration of existing material handling equipment. Large molding machine components are moved to the CMM by an overhead crane and can be easily placed within its measuring envelope.
Most of the production runs at Engel Canada are short, averaging about 10 pieces. Because of this, it's important that inspection results from a first-off piece are communicated quickly to the machine operator so offset adjustments to the machine can be made to keep parts within tolerance for the rest of the run.
"The CMM gives us that capability," said Jeff Bratt, machine shop quality control supervisor at Engel Canada. "We make a printout of the inspection results, mark it up, and send it back to the operator with the information he needs to correct his process. Before we had this capability, it was a lot more difficult to communicate process information to the operator," he said.
Since installing the BETA CMM, the setup inspection time for the larger parts has been reduced to about one hour. Bratt added that the CMM has also helped the company detect — much sooner than before — if a machine tool requires preventative maintenance because of its inability to hold tolerance.
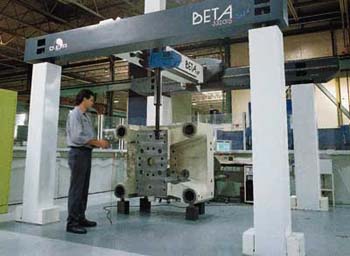
Best Fit Means Better Assembly
Engel uses a modular concept to build its machines. Design flexibility is applied to meet certain applications by configuring standard machine components to suit specific needs.
"We don't build a standard machine here," Bratt said. "Our market niche is the custom mold market. We have a standard base, but we have over 500 options that we put into machines, therefore each is quite different when it leaves the plant."
This modular approach to machine construction requires that subassemblies be checked for proper fit.
"We use the BETA to sort those components to give us the best assembly for certain applications," explained Bratt. "With the CMM, we've been able to put some smaller machines entirely within the measuring envelope and check the parallelism of components with the machine clamped up. If we're running into a problem with the machine functioning as it should, we can now move the whole machine assembly to the BETA and perform some critical alignment checks to make sure that components fit together properly."
As Engel Canada continues to grow and ramp up the number of machines it ships each year, there may be need for additional CMMs. "We know what coordinate metrology can do, and the payoff has been rather fast," Schock said. "In order to meet future production demands, we will be looking at replacing some other surface plate tools with a small CMM to handle smaller parts."