Fabricator Of Large Parts Upgrades From Remanufactured Sheffield To New Wenzel CMM
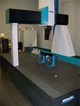
Wixom, MI - Maximizing business opportunities often times requires the evaluation of new capital expenditures to meet the customers' requirements. That is precisely what Olathe, Kansas-based Webco Manufacturing, Inc. experienced when a number of their good customers, including one of the major construction equipment manufacturers, awarded them new contracts that involved manufactured parts that exceeded their current CMM measuring capability.
Mike Miller, Webco manufacturing quality manager, explains, "Because quality and delivery were the major reasons why we were awarded the parts manufacturing contracts, the option of using outside CMM services was basically eliminated. The added transportation and handling costs added a level of unwanted time and expense that negatively impacted the profit margins and our accurate control of the delivery process."
Miller adds, "Having in-house CMM measuring capability is a significant asset in our fabrication business, and we soon realized that the remanufactured Sheffield RS150 CMM that we had recently purchased to meet the requirements for some of our new business, was not large enough for the subsequent new business we had secured.
Originally, we had purchased the remanufactured Sheffield RS150 equipped with OpenDMIS software from Xspect Solutions, Inc. Steve Cormier, sales manager of Xspect Solutions had initially provided a useful detailed evaluation of our metrology needs and the remanufactured Sheffield RS150 was selected at that time. When we had some problems with the remanufactured CMM, we were very impressed with Xspect's timely and professional service support for that machine. When we determined that the Sheffield CMM was not exactly what we needed, we again contacted Steve Cormier and explained what had changed and he personally met with us to make new recommendations. This time we agreed on the purchase of a new Wenzel 12.30.10, which we found to be very competitively priced even compared to similar rebuilt machines. We already had the suite of OpenDMIS software, so our programmers were experienced with its operation. In addition, we were offered a full trade-in value against the cost of the new machine and were allowed to keep the Sheffield in production during the four months prior to delivery. All in all, this has been a very pleasant customer/supplier relationship with excellent give and take on both sides. It's obvious why Xspect Solutions has become a major force in the CMM industry because you get a small business feeling about how they treat their customers, and that's important to a small business like ours."
Webco's Wenzel LH 12.30.10 has a measuring range of 1200 mm (X) x 3000 mm (Y) x 1000 mm (Z) with a standard accuracy with Renishaw TP200 Probe of U3 2.6+L300. The machine is equipped with a Renishaw PH10M/TP200 probe and a Wenzel WPC 2030 universal CMM controller that combines the latest CNC technology with the integration of all Renishaw heads with touch trigger probes. Large Wenzel CMM machines have a self-stabilizing design with integrated pneumatic vibration dampeners that eliminate the need for an isolated foundation. With the X bridge and Z ram manufactured of granite, identical thermal behavior can be predicted for all axes and accuracy maintained.
OpenDMIS is truly an intellectual software product that takes the guesswork out of CMM programming by seamlessly integrating CAD data with the CMM programming and measurement process, providing the user with a high level of power, precision and productivity at the single click of the mouse. Drag and dropping features from the database area into the adjacent programming window automatically generates the underlying DMIS 5.0 code together with probe and alignment definitions. Complex CMM programs can be created in a few minutes and simulated, utilizing the powerful simulation and collision avoidance tools standard in OpenDMIS. There are no pop-up windows in OpenDMIS. The product incorporates the use of dynamic sensitive tool bars, action icons and context sensitive work areas. The graphics view port remains freely visible at all times, maximizing operating efficiency. There are no windows to close and no cascading windows, and typical screen crowding is eliminated. Also, there is no annoying drill-down functionality.
SOURCE: Xspect Solutions, Inc.